Resumes
Resumes
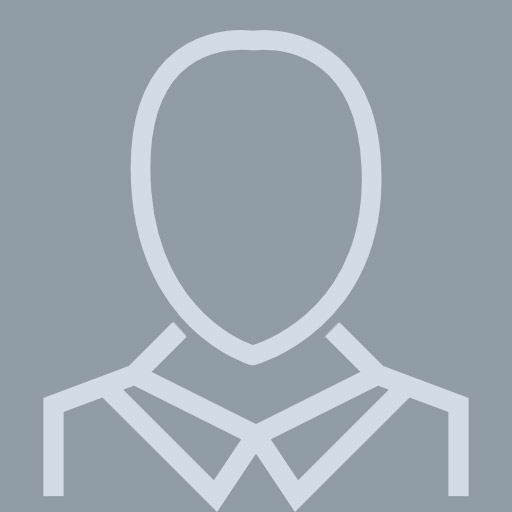
President
View pageLocation:
Santa Clara, CA
Industry:
Semiconductors
Work:
Adem
President
President
Education:
South - West Industrial University, Ukraine 1975 - 1980
Master of Science, Masters, Design
Master of Science, Masters, Design
Skills:
Engineering
Product Management
Manufacturing
Semiconductor Industry
Machining
Strategic Planning
Engineering Management
Product Development
Product Marketing
Semiconductors
Cross Functional Team Leadership
Electronics
Start Ups
Product Management
Manufacturing
Semiconductor Industry
Machining
Strategic Planning
Engineering Management
Product Development
Product Marketing
Semiconductors
Cross Functional Team Leadership
Electronics
Start Ups
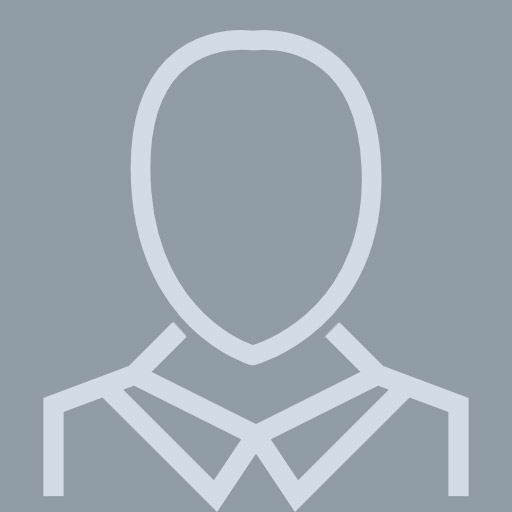
Mechanical Engineer
View pageLocation:
Santa Clara, CA
Industry:
Mechanical Or Industrial Engineering
Work:
Boris Kesil
Mechanical Engineer
Mechanical Engineer
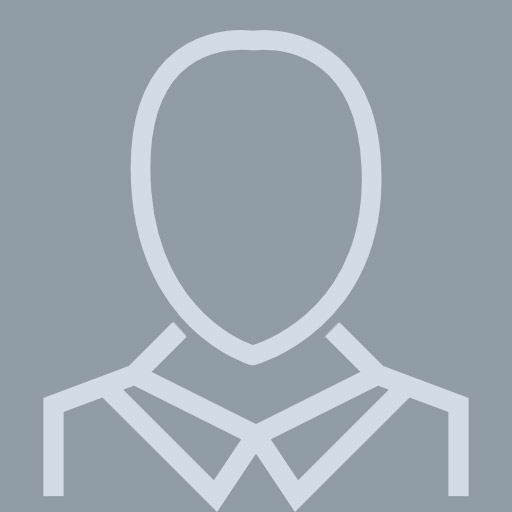
Boris Kesil
View pageLocation:
Santa Clara, CA
Industry:
Machinery
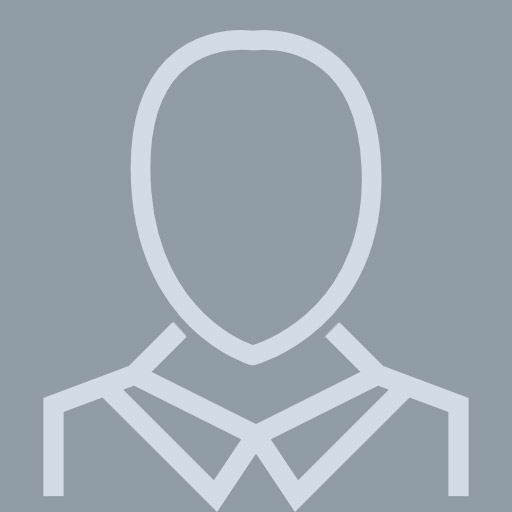