Resumes
Resumes
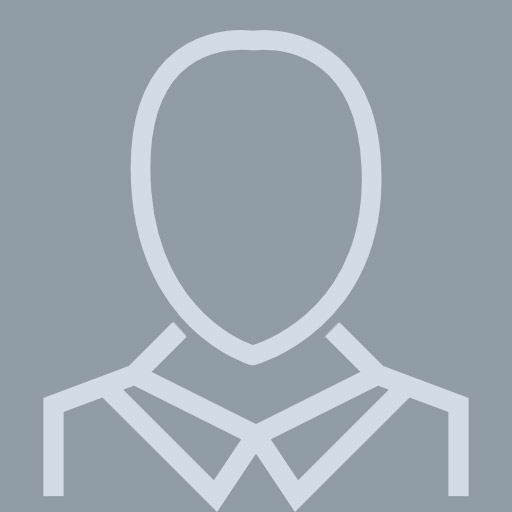
Applied Science Manager, Video Advertising
View pageLocation:
Bellevue, WA
Industry:
Computer Software
Work:
Amazon Web Services Dec 2017 - Nov 2018
Senior Data Scientist, Field and Partner Marketing
Microsoft Sep 2016 - Jul 2017
Senior Data Scientist, Web Platform Quality, Windows and Device Group
Microsoft Jun 1, 2015 - Sep 2016
Senior Software Engineer, Demand Forecasting, Microsoft Cloud Infrastructure and Operations
Tune Mar 2014 - Jun 2015
Senior Software Engineer, Dataflow, Mobile App Tracking
Boeing Oct 2012 - Feb 2014
Research Engineer, Level 5, Computer Simulation Focal
Senior Data Scientist, Field and Partner Marketing
Microsoft Sep 2016 - Jul 2017
Senior Data Scientist, Web Platform Quality, Windows and Device Group
Microsoft Jun 1, 2015 - Sep 2016
Senior Software Engineer, Demand Forecasting, Microsoft Cloud Infrastructure and Operations
Tune Mar 2014 - Jun 2015
Senior Software Engineer, Dataflow, Mobile App Tracking
Boeing Oct 2012 - Feb 2014
Research Engineer, Level 5, Computer Simulation Focal
Education:
University of Cincinnati 1995 - 1998
Doctorates, Doctor of Philosophy, Philosophy, Mechanical Engineering Shanghai Jiao Tong University 1992 - 1995
Masters, Electronics Engineering, Electronics Shanghai Jiao Tong University 1988 - 1992
Bachelors, Electronics Engineering, Electronics
Doctorates, Doctor of Philosophy, Philosophy, Mechanical Engineering Shanghai Jiao Tong University 1992 - 1995
Masters, Electronics Engineering, Electronics Shanghai Jiao Tong University 1988 - 1992
Bachelors, Electronics Engineering, Electronics
Skills:
Java
Cloud Computing
Statistical Modeling
Distributed Systems
Scala
Microsoft Office
Microsoft Excel
Apache Spark
Software Development
Finite Element Analysis
Simulations
Strategic Planning
C#
C++
Ansys
Microsoft Word
Apache Kafka
Automotive
Manufacturing
Azure Machine Learning
Python
R
C
Matlab
Autocad
Team Building
Customer Service
Machine Learning
Optimization
Forecasting
Process Simulation
Amazon Web Services
Powerbi
Tableau
Monte Carlo Simulation
Hadoop
Cloud Computing
Statistical Modeling
Distributed Systems
Scala
Microsoft Office
Microsoft Excel
Apache Spark
Software Development
Finite Element Analysis
Simulations
Strategic Planning
C#
C++
Ansys
Microsoft Word
Apache Kafka
Automotive
Manufacturing
Azure Machine Learning
Python
R
C
Matlab
Autocad
Team Building
Customer Service
Machine Learning
Optimization
Forecasting
Process Simulation
Amazon Web Services
Powerbi
Tableau
Monte Carlo Simulation
Hadoop
Certifications:
Design For Six Sigma, Black Belt
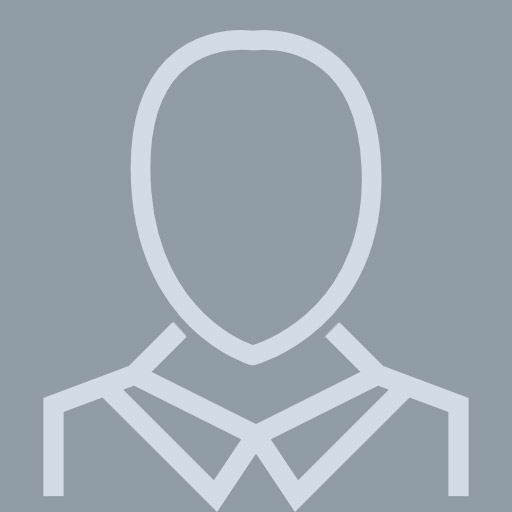
Xinyu Zhou
View page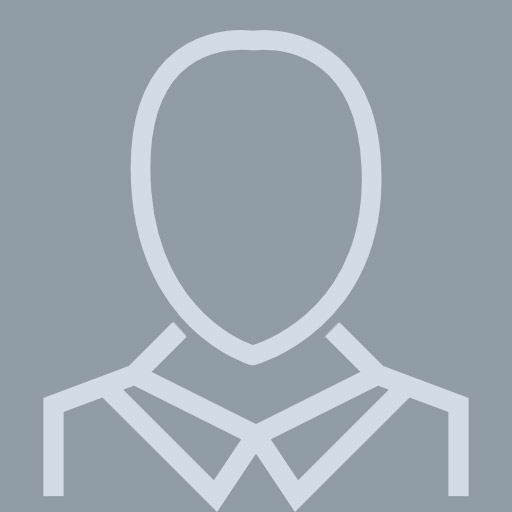
Xinyu Zhou Salt Lake City, UT
View pageWork:
Goldman Sachs
Salt Lake City, UT
May 2010 to Mar 2012
Senior Analyst Developer
VMWare
Palo Alto, CA
Mar 2008 to May 2010
Software Engineer
Arizona State University
Jul 2004 to Dec 2007
Research Assistant and Teaching Assistant
Translational Genomics Research Institute (TGen)
Phoenix, AZ
May 2007 to Aug 2007
Research Intern
Google
Mountain View, CA
May 2006 to Aug 2006
Software Engineer Intern
Salt Lake City, UT
May 2010 to Mar 2012
Senior Analyst Developer
VMWare
Palo Alto, CA
Mar 2008 to May 2010
Software Engineer
Arizona State University
Jul 2004 to Dec 2007
Research Assistant and Teaching Assistant
Translational Genomics Research Institute (TGen)
Phoenix, AZ
May 2007 to Aug 2007
Research Intern
Mountain View, CA
May 2006 to Aug 2006
Software Engineer Intern
Education:
Arizona State University
Feb 2008
PhD in Computer Science and Engineering
South China University of Technology
May 2004
Master in Computer Science and Engineering
Feb 2008
PhD in Computer Science and Engineering
South China University of Technology
May 2004
Master in Computer Science and Engineering