Resumes
Resumes
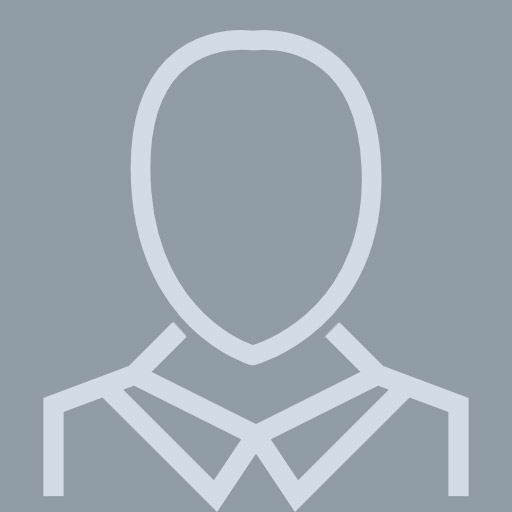
Pvd Process Development Manager At Oem Group, Inc
View pageLocation:
2120 west Guadalupe Rd, Gilbert, AZ 85233
Industry:
Semiconductors
Work:
Oem Group, Inc.
Pvd Process Development Manager at Oem Group, Inc
Tegal Corporation Aug 2002 - Mar 2010
Pvd Process Development Manager
Sputtered Films Inc Jan 2002 - Aug 2002
Pvd Process Development Manager
Sputtered Films Inc Jan 2000 - Jan 2002
Senior Scientist
Sputtered Films Inc Nov 1997 - Jan 2000
Process Development Engineer
Pvd Process Development Manager at Oem Group, Inc
Tegal Corporation Aug 2002 - Mar 2010
Pvd Process Development Manager
Sputtered Films Inc Jan 2002 - Aug 2002
Pvd Process Development Manager
Sputtered Films Inc Jan 2000 - Jan 2002
Senior Scientist
Sputtered Films Inc Nov 1997 - Jan 2000
Process Development Engineer
Education:
Institute of High - Current Electronics (Tomsk, Russia) 1984 - 1989
Doctorates, Doctor of Philosophy, Philosophy Ryzan Radio Engineering Academy 1972 - 1977
Master of Science, Masters
Doctorates, Doctor of Philosophy, Philosophy Ryzan Radio Engineering Academy 1972 - 1977
Master of Science, Masters
Skills:
Engineering Management
Semiconductors
Semiconductor Industry
Process Simulation
Pvd
Thin Films
Metrology
Failure Analysis
Design of Experiments
Photolithography
Cvd
Spc
Silicon
Ic
Mems
R&D
Plasma Etch
Electronics
Characterization
Nanotechnology
Cmos
Pecvd
Labview
Etching
Semiconductors
Semiconductor Industry
Process Simulation
Pvd
Thin Films
Metrology
Failure Analysis
Design of Experiments
Photolithography
Cvd
Spc
Silicon
Ic
Mems
R&D
Plasma Etch
Electronics
Characterization
Nanotechnology
Cmos
Pecvd
Labview
Etching
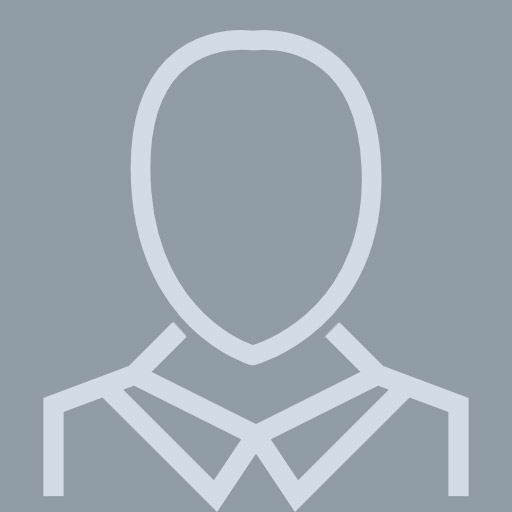
Institute Of High-Current
View pageLocation:
Goleta, CA
Work:
Institute of High-Current
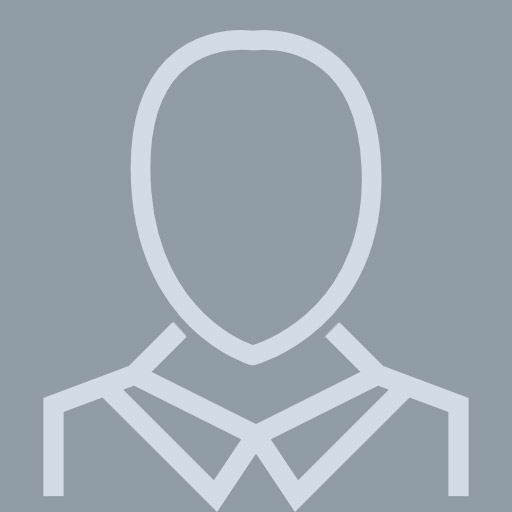
Valery Felmetsger
View pageLocation:
Goleta, CA