Resumes
Resumes
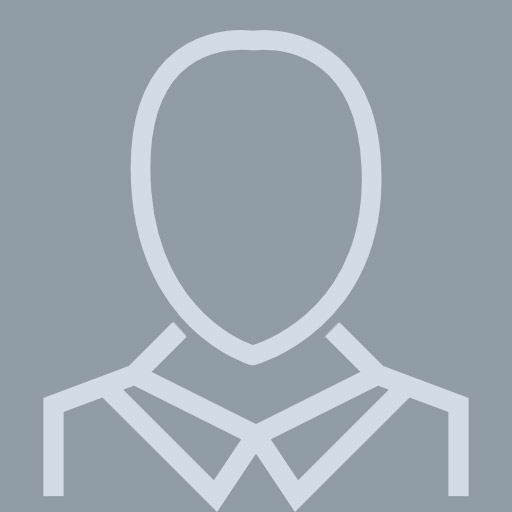
Thomas King Old Saybrook, CT
View pageWork:
WELLPOINT, INC
New York, NY
2005 to May 2013
Director, Marketing, Open Enrollment and Event Planning
UNITED HEALTHCARE
Minnetonka, MN
2004 to 2005
Director, Marketing Proposal Services
AETNA HEALTH CARE
Middletown, CT
2003 to 2004
Senior Manager, National Accounts Sales Support
CIGNA CORPORATION, Bloomfield
2000 to 2003
Director, National Accounts Sales Support
CIGNA CORPORATION, Bloomfield
Hartford, CT
1996 to 2003
CIGNA CORPORATION, Bloomfield
1998 to 2000
Assistant Director, Market Research
CIGNA CORPORATION, Bloomfield
1996 to 1998
Manager, New Business Development
MARRIOTT HOTELS
Shelton, CT
1992 to 1995
Director of Sales and Marketing
New York, NY
2005 to May 2013
Director, Marketing, Open Enrollment and Event Planning
UNITED HEALTHCARE
Minnetonka, MN
2004 to 2005
Director, Marketing Proposal Services
AETNA HEALTH CARE
Middletown, CT
2003 to 2004
Senior Manager, National Accounts Sales Support
CIGNA CORPORATION, Bloomfield
2000 to 2003
Director, National Accounts Sales Support
CIGNA CORPORATION, Bloomfield
Hartford, CT
1996 to 2003
CIGNA CORPORATION, Bloomfield
1998 to 2000
Assistant Director, Market Research
CIGNA CORPORATION, Bloomfield
1996 to 1998
Manager, New Business Development
MARRIOTT HOTELS
Shelton, CT
1992 to 1995
Director of Sales and Marketing
Education:
University of Southern California
Los Angeles, CA
2013 to 2015
Masters in Health Administration
Burke Institute
Chicago, IL
2001 to 2013
Certification in Qualitative and Quantitative Analysis
Central Connecticut State University
New Britain, CT
Bachelors in Communications
Los Angeles, CA
2013 to 2015
Masters in Health Administration
Burke Institute
Chicago, IL
2001 to 2013
Certification in Qualitative and Quantitative Analysis
Central Connecticut State University
New Britain, CT
Bachelors in Communications
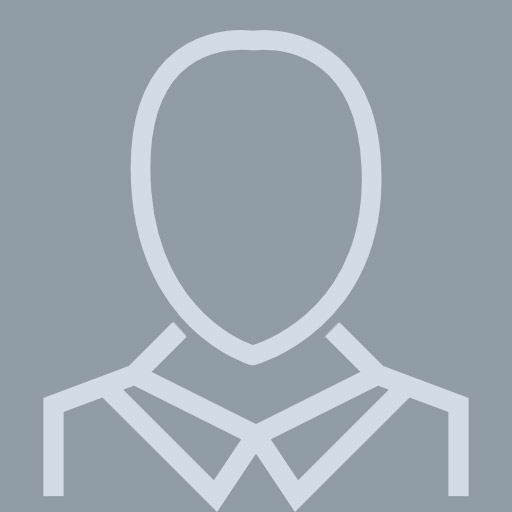
Thomas King Duluth, GA
View pageWork:
Prairie Capital
Chicago, IL
Jun 2013 to Aug 2013
Intern/Financial Analyst
Goodwill of North Georgia
Lawrenceville, GA
Sep 2012 to Dec 2012
Production Associate
Little Salad Shop
New Haven, CT
Jun 2011 to Dec 2011
Production Prep and Delivery/Utility
Stonebrier Stingrays
Suwanee, GA
May 2008 to Aug 2010
Assistant Swim Coach
Chicago, IL
Jun 2013 to Aug 2013
Intern/Financial Analyst
Goodwill of North Georgia
Lawrenceville, GA
Sep 2012 to Dec 2012
Production Associate
Little Salad Shop
New Haven, CT
Jun 2011 to Dec 2011
Production Prep and Delivery/Utility
Stonebrier Stingrays
Suwanee, GA
May 2008 to Aug 2010
Assistant Swim Coach
Education:
Yale College
New Haven, CT
2009 to 2013
Bachelor of Arts, Expected May 2017 in Economics
New Haven, CT
2009 to 2013
Bachelor of Arts, Expected May 2017 in Economics
Skills:
Computer Skills: Excel, PowerPoint, Word, HTML, Dreamweaver, and STATA
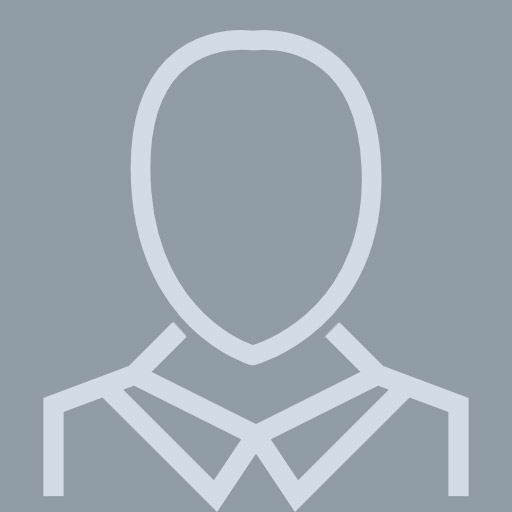
Thomas King Memphis, TN
View pageWork:
Hardee's
Rantoul, IL
Apr 2012 to Mar 2013
Cashier
Target
Chicago, IL
Oct 2010 to Jan 2011
Team Member / Cashier/ Seasonal
Michaels Arts and Crafts
Chicago, IL
Jun 2010 to Sep 2010
Sales Assoicate / Seasonal
Jimmy Johns
Chicago, IL
Apr 2007 to Oct 2008
Cashier
Rantoul, IL
Apr 2012 to Mar 2013
Cashier
Target
Chicago, IL
Oct 2010 to Jan 2011
Team Member / Cashier/ Seasonal
Michaels Arts and Crafts
Chicago, IL
Jun 2010 to Sep 2010
Sales Assoicate / Seasonal
Jimmy Johns
Chicago, IL
Apr 2007 to Oct 2008
Cashier
Education:
Mount Carmel High School
Chicago, IL
Sep 2003 to May 2007
Diploma
Harold Washington College
Chicago, IL
Chicago, IL
Sep 2003 to May 2007
Diploma
Harold Washington College
Chicago, IL
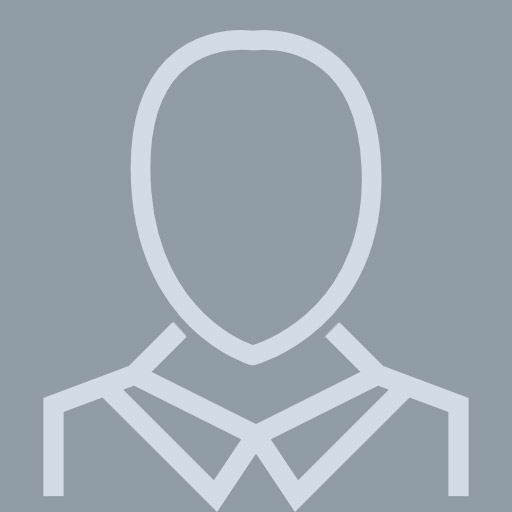
Thomas King Lisle, IL
View pageWork:
URS at Fermilab
Batavia, IL
Sep 2008 to Dec 2012
Senior Project Quality Engineer
IS and R Services
Lisle, IL
2008 to 2008
Corporate Trainer
Benedictine University
Lisle, IL
2007 to 2008
Adjunct Professor
Rubicon Technologies
Franklin Park, IL
2007 to 2007
Facilities Management and Process Improvement
Convergent Technologies
Burr Ridge, IL
2005 to 2006
Project Manager and Research Engineer,
WindChannel Communications
Raleigh, NC
1999 to 2005
VP and Principal Technologist
Vishay, Inc
West Palm Beach, FL
1997 to 1999
Senior Scientist
Implant Innovations, Inc.
Palm Beach Gardens, FL
1996 to 1997
Sr. Engineer/Staff Scientist
MWM Services
Riviera Beach, FL
1994 to 1996
Management/Engineering Consultant
Pratt Whitney - United Technologies
West Palm Beach, FL
1984 to 1993
Project Manager/Senior Materials Engineer
Batavia, IL
Sep 2008 to Dec 2012
Senior Project Quality Engineer
IS and R Services
Lisle, IL
2008 to 2008
Corporate Trainer
Benedictine University
Lisle, IL
2007 to 2008
Adjunct Professor
Rubicon Technologies
Franklin Park, IL
2007 to 2007
Facilities Management and Process Improvement
Convergent Technologies
Burr Ridge, IL
2005 to 2006
Project Manager and Research Engineer,
WindChannel Communications
Raleigh, NC
1999 to 2005
VP and Principal Technologist
Vishay, Inc
West Palm Beach, FL
1997 to 1999
Senior Scientist
Implant Innovations, Inc.
Palm Beach Gardens, FL
1996 to 1997
Sr. Engineer/Staff Scientist
MWM Services
Riviera Beach, FL
1994 to 1996
Management/Engineering Consultant
Pratt Whitney - United Technologies
West Palm Beach, FL
1984 to 1993
Project Manager/Senior Materials Engineer
Education:
Florida State University
Tallahassee, FL
1978 to 1984
Ph.D. in Analytical Chemistry, Materials Science, Data Enhancement and Communication
University of Maryland
College Park, MD
1974 to 1978
M.S. in Analytical Chemistry, Biochemistry, Clinical Chemistry, Data Acquisition and Enhancement
Southern Illinois University
Carbondale, IL
1968 to 1974
B.A. and A.A. in Chemistry and Aviation Technology
Tallahassee, FL
1978 to 1984
Ph.D. in Analytical Chemistry, Materials Science, Data Enhancement and Communication
University of Maryland
College Park, MD
1974 to 1978
M.S. in Analytical Chemistry, Biochemistry, Clinical Chemistry, Data Acquisition and Enhancement
Southern Illinois University
Carbondale, IL
1968 to 1974
B.A. and A.A. in Chemistry and Aviation Technology
Skills:
The following comprise my efforts managing quality and improvement centric projects: QA involved identifying appropriate production methods, testing procedures (ANSI, ASTM, EPA), metrics and tolerances, developing new procedures (mechanical, chemical, or testing), maintaining project/ process configuration, calibration control of instrumentation, and traceability of standards (chemical and metrological). QA also included evaluation of projects or vendors quality programs and technical capability, their adherence to process requirements and procedures, and evaluation/approval of their process change requests. Processes were proactively evaluated for risks and weaknesses to ensure adequate controls were incorporated. QC involved assessments of pre and post process materials for compliance to chemical specifications (elemental and molecular composition, hazardous waste disposition), physical specifications (GD&T, hardness, phase transitions), the maintenance of process set-up and process control (SOPs, lot traceability, and record maintenance), monitoring process independent variables (time, temperature, pressure, speed-feed, scheduled tool changes), data quality (accuracy/precision, S/N, Nyquist, BER), and monitoring dependent variables (SPC). Failure analysis involved identifying the failure or nonconformance root cause in scrap, field failures or engineering testing. Failure analysis included methods employed in QC testing and, frequently, high-magnification imaging and micro-quantitative analysis. Process improvement opportunities were identified by evaluating process capability and reviewing rolled throughput yield, rework, scrap, costs and schedules. Improvement required integration of alternative technology or development of new technology optimized by design of experiments to expedite process development and ensure well characterized process variables. Processes and methods were improved by minimizing bureaucracy and optimizing or deleting testing, metrics, and instructions/documentation/ records as appropriate. Training was provided to personnel to understand, identify, and perform process improvement (6-Sigma & Lean). Process improvement projects involved functionality diverse disciplines and were multi-million dollar technology/R&D efforts; projects were managed using systematic standard principles to ensure cost, schedule, deliverables and quality were achieved within project scope. Decommissioning involved closure of projects/facilities and ensuring item control (equipment) and concomitant risks (hazardous wastes) were identified and safely and appropriately addressed. Decommissioning required coaching and reviewing the development of high-level plans/guidelines for adherence to regulations for identification and disposal of assets and hazardous materials, ensuring safety and training, and consideration of alternative actions and adaptive planning for unknowns.