Resumes
Resumes
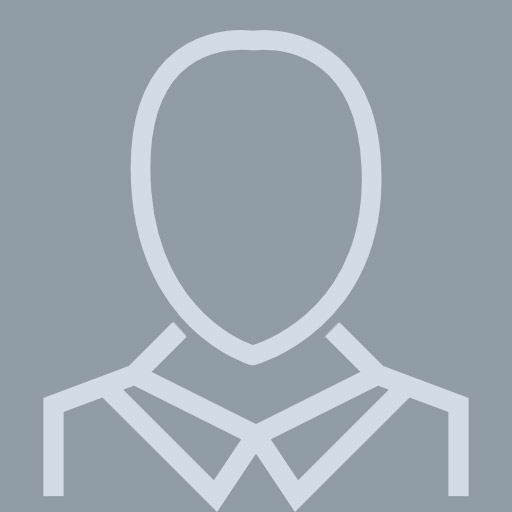
Engineering Contractor
View pageLocation:
6 Strawberry Ln, Hudson, MA 01749
Industry:
Mechanical Or Industrial Engineering
Work:
Sterling Engineering Sullair
Engineering Contractor
Sterling Engineering/Sullair Jan 2015 - Dec 2015
Senior Mechanical Engineer Contractor
Ktr Group Worldwide Jan 2012 - Nov 2013
Engineering Product Manager
Sengenuity Feb 2010 - Dec 2011
Senior Mechanical Engineering Consultant
Setra Systems Mar 2003 - Aug 2009
Product Marketing Manager
Engineering Contractor
Sterling Engineering/Sullair Jan 2015 - Dec 2015
Senior Mechanical Engineer Contractor
Ktr Group Worldwide Jan 2012 - Nov 2013
Engineering Product Manager
Sengenuity Feb 2010 - Dec 2011
Senior Mechanical Engineering Consultant
Setra Systems Mar 2003 - Aug 2009
Product Marketing Manager
Education:
Clark University 1983 - 1988
Master of Business Administration, Masters University of Florida
Bachelor of Science In Aerospace Engineering, Bachelors, Aerospace Engineering
Master of Business Administration, Masters University of Florida
Bachelor of Science In Aerospace Engineering, Bachelors, Aerospace Engineering
Skills:
Engineering
Product Development
Manufacturing
Mechanical Engineering
Hydraulics
Engineering Management
Product Management
Product Marketing
Product Design
Sales
Petroleum
Solidworks
Pro Engineer
Labview
Competitive Analysis
Lean Manufacturing
Product Development
Manufacturing
Mechanical Engineering
Hydraulics
Engineering Management
Product Management
Product Marketing
Product Design
Sales
Petroleum
Solidworks
Pro Engineer
Labview
Competitive Analysis
Lean Manufacturing