Resumes
Resumes
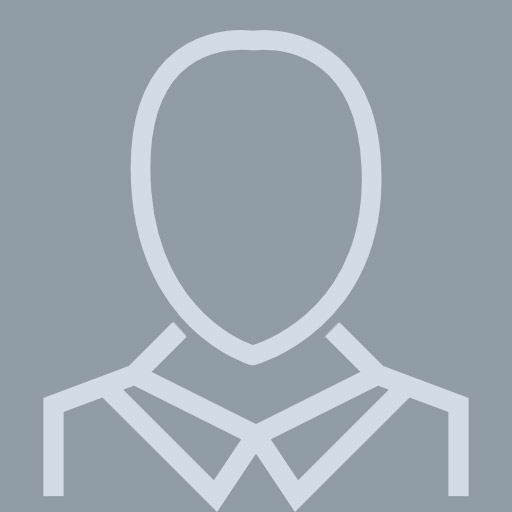
Mechenical Detailer And Drafter
View pageLocation:
San Francisco, CA
Industry:
Mechanical Or Industrial Engineering
Work:
Beahm Designs
Mechenical Detailer and Drafter
Cobham 2005 - 2013
Drafer Ii
Bizlink Technology 2001 - 2005
Engineeing Technician and Drafter
Mechenical Detailer and Drafter
Cobham 2005 - 2013
Drafer Ii
Bizlink Technology 2001 - 2005
Engineeing Technician and Drafter
Education:
Heald College 1999 - 1999
Associates Chabot College 1997 - 1997
Associates Chabot College 1997 - 1997
Skills:
Cad
Autocad
Solidworks
Adobe Acrobat
Microsoft Office
Modeling
Photoshop
Sheet Metal
Manufacturing
Gd&T
Pore
Orcad
Pointman Database
Iso
Design For Manufacturing
Ptc Creo
Engineering
Pro Engineer
Software Documentation
Lean Manufacturing
Eco Processing
Design Conception
Design Cad Process
Autocad
Solidworks
Adobe Acrobat
Microsoft Office
Modeling
Photoshop
Sheet Metal
Manufacturing
Gd&T
Pore
Orcad
Pointman Database
Iso
Design For Manufacturing
Ptc Creo
Engineering
Pro Engineer
Software Documentation
Lean Manufacturing
Eco Processing
Design Conception
Design Cad Process
Interests:
Photography
Ping Pong
Swimming
Ping Pong
Swimming
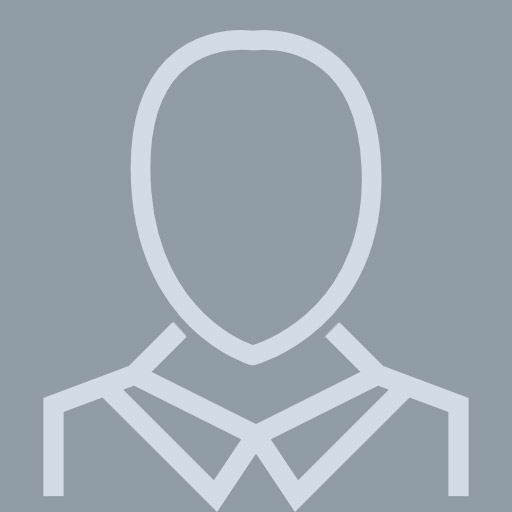