Resumes
Resumes
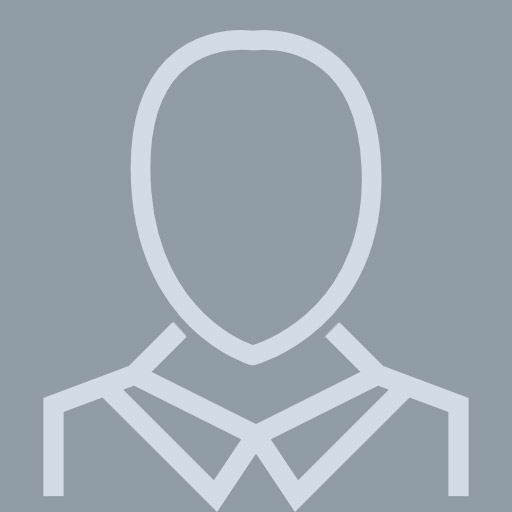
Senior Manufacturing Engineer
View pageLocation:
15819 Haven Dr, Macomb, MI 48042
Industry:
Automotive
Work:
Oakland University Jan 2010 - May 2010
Adjunct Professor, Advanced Machining
General Motors Jun 2005 - Jan 2007
Process Engineer
General Motors Jun 2005 - Jan 2007
Senior Manufacturing Engineer
General Motors Jun 2003 - Jun 2005
Fastening Engineer
General Motors Jun 2002 - Jun 2003
Production Supervisor
Adjunct Professor, Advanced Machining
General Motors Jun 2005 - Jan 2007
Process Engineer
General Motors Jun 2005 - Jan 2007
Senior Manufacturing Engineer
General Motors Jun 2003 - Jun 2005
Fastening Engineer
General Motors Jun 2002 - Jun 2003
Production Supervisor
Education:
Oakland University 2005 - 2009
Doctorates, Doctor of Philosophy, Philosophy, Mechanical Engineering Oakland University 2002 - 2004
Master of Science, Masters, Mechanical Engineering Oakland University 1997 - 2001
Bachelors, Bachelor of Science, Mechanical Engineering
Doctorates, Doctor of Philosophy, Philosophy, Mechanical Engineering Oakland University 2002 - 2004
Master of Science, Masters, Mechanical Engineering Oakland University 1997 - 2001
Bachelors, Bachelor of Science, Mechanical Engineering
Skills:
Machining
Finite Element Analysis
Automotive
Engineering
Automotive Engineering
Machine Tools
Quality Control
Metal Cutting Force Simulation
Powertrain
Manufacturing
Continuous Improvement
Unigraphics
Lean Manufacturing
Machining Throughput Optimization
Fea Machining Analysis
Tooling Optimzation
Components
Machining Quality Analysis
Finite Element Analysis
Automotive
Engineering
Automotive Engineering
Machine Tools
Quality Control
Metal Cutting Force Simulation
Powertrain
Manufacturing
Continuous Improvement
Unigraphics
Lean Manufacturing
Machining Throughput Optimization
Fea Machining Analysis
Tooling Optimzation
Components
Machining Quality Analysis