Resumes
Resumes
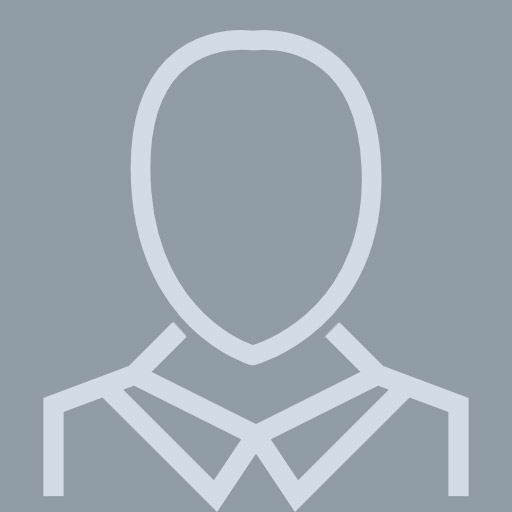
Administrative Support Coordinator
View pageLocation:
Tucson, AZ
Industry:
Hospital & Health Care
Work:
Tucson Medical Center
Administrative Support Coordinator
Administrative Support Coordinator
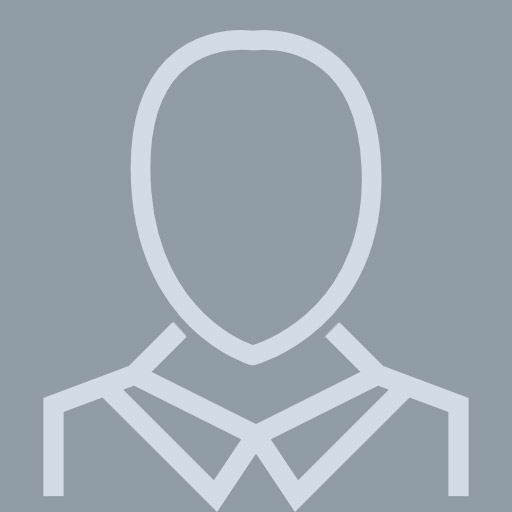
Administrative Support Coordinator
View pageLocation:
Tucson, AZ
Industry:
Hospital & Health Care
Work:
Tucson Medical Center
Administrative Support Coordinator
Tmc Healthcare
Administrative Support Coordinator
Administrative Support Coordinator
Tmc Healthcare
Administrative Support Coordinator
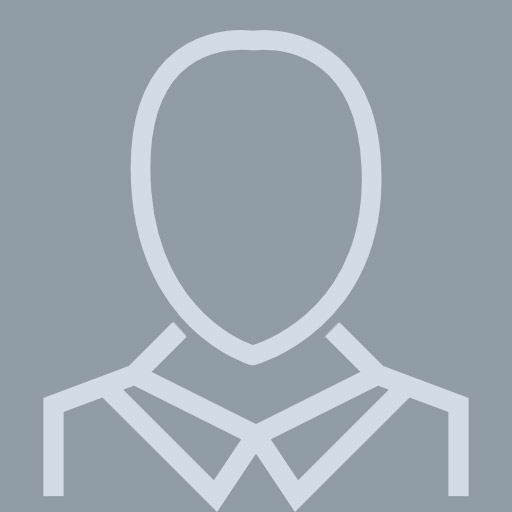