Resumes
Resumes
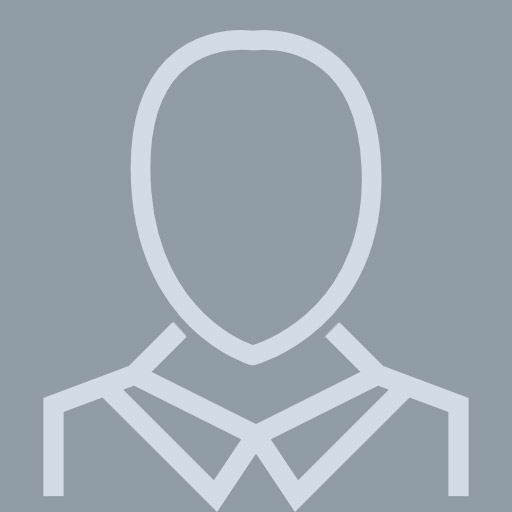
Phillip Dowson
View pageLocation:
Greensburg, PA
Industry:
Information Technology And Services
Work:
Materials Engineering Services
Semi Retired
Semi Retired
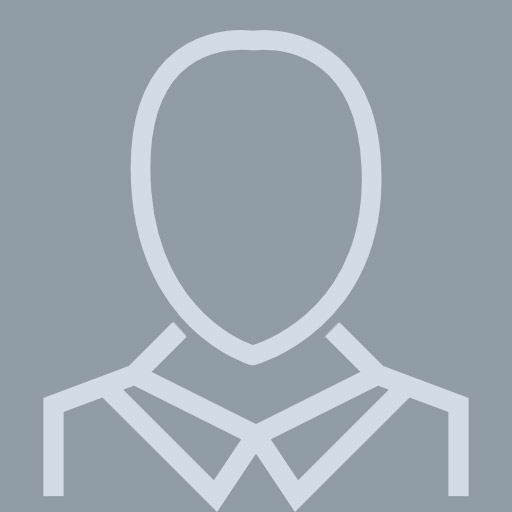
Manager Maeterials Engineer
View pageLocation:
Greensburg, PA
Industry:
Machinery
Work:
Elliott Fgroup
Manager Maeterials Engineer
Manager Maeterials Engineer
Skills:
Project Engineering
Engineering
Pumps
Energy
Power Generation
Gas Turbines
Power Plants
Mechanical Engineering
Failure Analysis
Remaining Life Assessment
Defect Tolerant Design Concepts
Expert In Corrosion and Fouling Resistant Coatings
Application of Abradable and Rub Tolerant Seals
Selection of Materials and Welding Design
Engineering
Pumps
Energy
Power Generation
Gas Turbines
Power Plants
Mechanical Engineering
Failure Analysis
Remaining Life Assessment
Defect Tolerant Design Concepts
Expert In Corrosion and Fouling Resistant Coatings
Application of Abradable and Rub Tolerant Seals
Selection of Materials and Welding Design