Resumes
Resumes
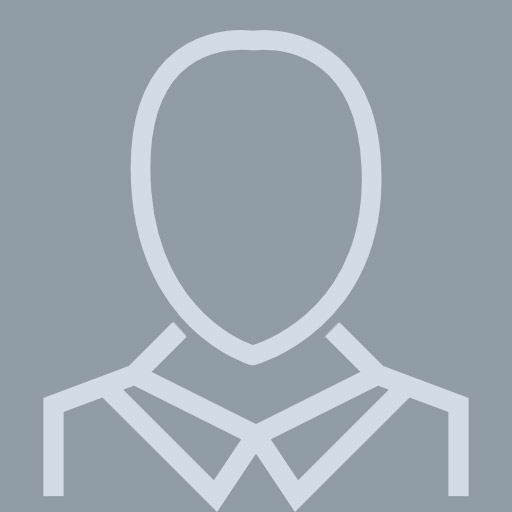
Georgia Carolina Council Commissioner
View pageLocation:
136 Sweetbay Dr, Aiken, SC 29803
Industry:
Research
Work:
Boy Scouts of America
Georgia Carolina Council Commissioner
Allison Gas Turbine Rolls Royce North America Sep 1, 1992 - May 1, 1998
Material Engineer
Savannah River Nuclear Solutions Sep 1, 1992 - May 1, 1998
Senior Fellow Scientist
Rensselaer Polytechnic Institute Aug 1987 - Aug 1992
Research Assistant
Georgia Carolina Council Commissioner
Allison Gas Turbine Rolls Royce North America Sep 1, 1992 - May 1, 1998
Material Engineer
Savannah River Nuclear Solutions Sep 1, 1992 - May 1, 1998
Senior Fellow Scientist
Rensselaer Polytechnic Institute Aug 1987 - Aug 1992
Research Assistant
Education:
Rensselaer Polytechnic Institute 1987 - 1992
Doctorates, Doctor of Philosophy, Materials Science, Engineering, Philosophy Missouri University of Science and Technology 1982 - 1987
Bachelors, Bachelor of Science, Metallurgical Engineering Seward High School
Doctorates, Doctor of Philosophy, Materials Science, Engineering, Philosophy Missouri University of Science and Technology 1982 - 1987
Bachelors, Bachelor of Science, Metallurgical Engineering Seward High School
Skills:
Materials Science
Materials
Composites
Corrosion
R&D
Powder X Ray Diffraction
Coatings
Process Engineering
Scanning Electron Microscopy
Chemical Engineering
Nanotechnology
Spectroscopy
Experimentation
Metallurgy
Catalysis
Alloys
Chemistry
Statistics
Research and Development
Science
Root Cause Analysis
Gas Permeation
Physical Metallurgy
Xrd
Research and Development
Materials
Composites
Corrosion
R&D
Powder X Ray Diffraction
Coatings
Process Engineering
Scanning Electron Microscopy
Chemical Engineering
Nanotechnology
Spectroscopy
Experimentation
Metallurgy
Catalysis
Alloys
Chemistry
Statistics
Research and Development
Science
Root Cause Analysis
Gas Permeation
Physical Metallurgy
Xrd
Research and Development
Interests:
Politics
Science and Technology
Children
Education
Science and Technology
Children
Education
Languages:
English