Resumes
Resumes
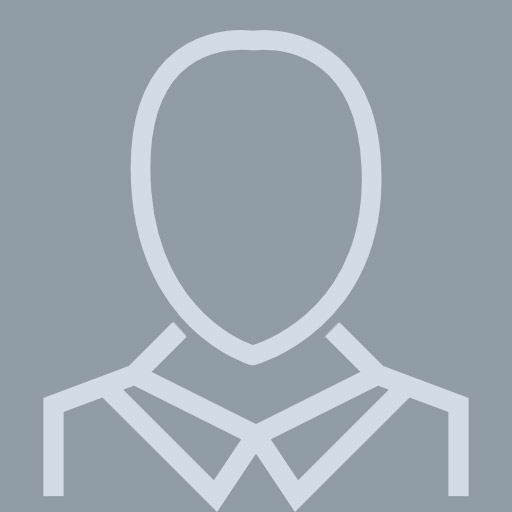
President At Morren Plastic Molding
View pageLocation:
7677 Fillmore St, Allendale, MI 49401
Industry:
Plastics
Work:
Morren Plastic Molding
President at Morren Plastic Molding
President at Morren Plastic Molding
Skills:
Plastics
Injection Molding
Manufacturing
Continuous Improvement
Machine Tools
Purchasing
Molding
Extrusion
Composites
Injection Molding
Manufacturing
Continuous Improvement
Machine Tools
Purchasing
Molding
Extrusion
Composites