Resumes
Resumes
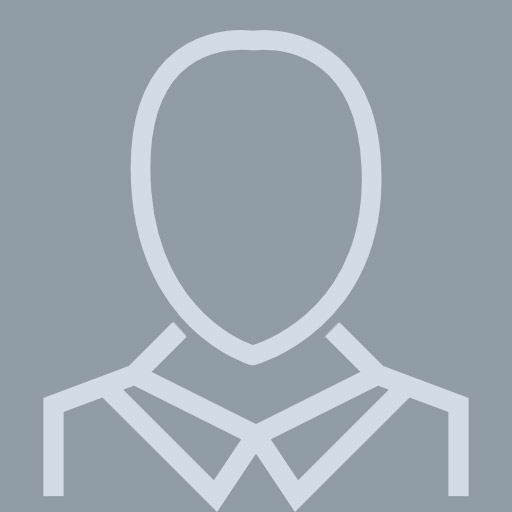
Director, Strategic Innovation
View pagePosition:
Director, Strategic Innovation at Autodesk, Faculty at Singularity University
Location:
San Francisco Bay Area
Industry:
Design
Work:
Autodesk - San Francisco Bay Area since Sep 2010
Director, Strategic Innovation
Singularity University since May 2012
Faculty
Autodesk Jan 2001 - Mar 2007
Creative Director
Marine Advanced Research Feb 2000 - Feb 2007
Design and Engineering Consultant. Test Pilot
SWERVE CO Dec 1999 - Jan 2001
Vice President
Director, Strategic Innovation
Singularity University since May 2012
Faculty
Autodesk Jan 2001 - Mar 2007
Creative Director
Marine Advanced Research Feb 2000 - Feb 2007
Design and Engineering Consultant. Test Pilot
SWERVE CO Dec 1999 - Jan 2001
Vice President
Education:
Singularity University 2012 - 2012
Executive Program, Exponential Technologies Harvard Business School 2006 - 2006
University of California, Santa Cruz 1989 - 1992
Bachelor, History
Executive Program, Exponential Technologies Harvard Business School 2006 - 2006
University of California, Santa Cruz 1989 - 1992
Bachelor, History
Skills:
Business Development
Entrepreneurship
Interaction Design
User Experience Design
Experience Design
Corporate Strategy
Design Strategy
Digital Manufacturing
Design Thinking
Future Trends
Innovation
Entrepreneurship
Interaction Design
User Experience Design
Experience Design
Corporate Strategy
Design Strategy
Digital Manufacturing
Design Thinking
Future Trends
Innovation
Interests:
Extensive business experience in China, Japan, Singapore, U.S.A. and throughout Western Europe.
Fluent English, French and Italian. Rudiments of Spanish and Japanese.
U.S. and E.U. Citizenship.
Honor & Awards:
Clio, Rebrand 100, IDSA IDEA, New Media Invision
United Nations IMO Medal for Exceptional Bravery at Sea, 2009
New Zealand Bravery Medal, 2010
United States Coast Guard Citation for Bravery, 2011
Rod Stephens Trophy, 2009
Languages:
French
Italian
Spanish
Italian
Spanish