Resumes
Resumes
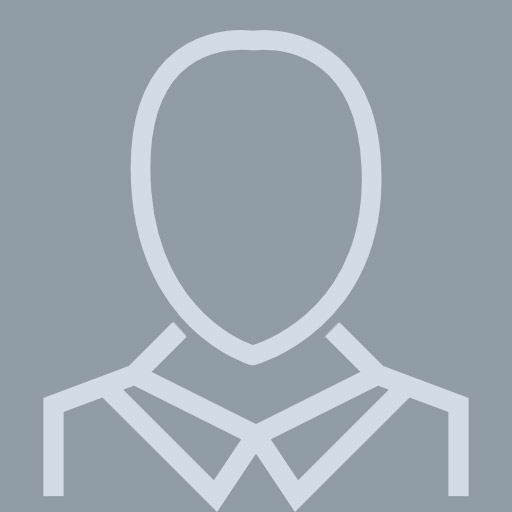
Alloys And Process Development Discipline Chief
View pageLocation:
9 Claire Rd, Vernon, CT 06066
Industry:
Aviation & Aerospace
Work:
Pratt & Whitney
Alloys and Process Development Discipline Chief
Pratt & Whitney Apr 2011 - Apr 2012
Staff Engineer - Materials
Pratt & Whitney Apr 2008 - Apr 2011
Senior Materials Engineer
Pratt & Whitney Jan 2005 - Apr 2008
Materials Engineer
Carpenter Technology Mar 2001 - Jan 2005
Process and Facilities Engineer
Alloys and Process Development Discipline Chief
Pratt & Whitney Apr 2011 - Apr 2012
Staff Engineer - Materials
Pratt & Whitney Apr 2008 - Apr 2011
Senior Materials Engineer
Pratt & Whitney Jan 2005 - Apr 2008
Materials Engineer
Carpenter Technology Mar 2001 - Jan 2005
Process and Facilities Engineer
Education:
University of Connecticut 2011 - 2014
Doctorates, Doctor of Philosophy, Engineering, Philosophy University of Connecticut 2006 - 2009
Master of Science, Masters, Engineering Alfred University 1996 - 2000
Bachelors, Bachelor of Science, Engineering
Doctorates, Doctor of Philosophy, Engineering, Philosophy University of Connecticut 2006 - 2009
Master of Science, Masters, Engineering Alfred University 1996 - 2000
Bachelors, Bachelor of Science, Engineering
Skills:
Six Sigma
Continuous Improvement
Heat Treatment
Characterization
Lean Manufacturing
Design of Experiments
Materials Science
Program Management
Failure Analysis
Composites
Materials
Coatings
Alloys
Metallurgy
Six Sigma Black Belt
Utc Ace Certification
Unigraphics
Invstment Casting
Financial Reporting
Preparation of Business Cases
Proposal Writing
Report Writing
Investment Casting
Superalloys
Thermal Barrier Coatings
Continuous Improvement
Heat Treatment
Characterization
Lean Manufacturing
Design of Experiments
Materials Science
Program Management
Failure Analysis
Composites
Materials
Coatings
Alloys
Metallurgy
Six Sigma Black Belt
Utc Ace Certification
Unigraphics
Invstment Casting
Financial Reporting
Preparation of Business Cases
Proposal Writing
Report Writing
Investment Casting
Superalloys
Thermal Barrier Coatings
Interests:
Photography
Wood Working
Computers
Salt Water Aquariums
Wood Working
Computers
Salt Water Aquariums
Certifications:
Six Sigma Black Belt
Carpenter Technology Corporation
Carpenter Technology Corporation