Resumes
Resumes
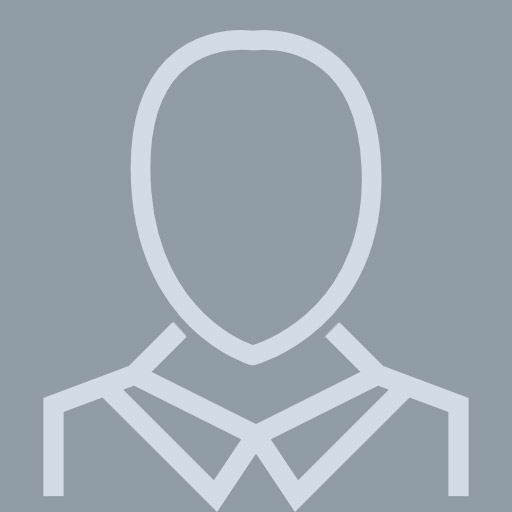
Product Development Manager
View pageLocation:
Akron, OH
Industry:
Plastics
Work:
Piranha Hose Products Inc
Product Development Manager
Eaton Jan 2008 - Oct 2011
Product Development Manager Engineering Specialist
Saint-Gobain 2004 - 2008
Product Development Manager
Saint-Gobain 2002 - 2007
Product Manager
Saint-Gobain Performance Plastics Oct 1997 - Aug 2002
Product Development and Applications Engineering Manager
Product Development Manager
Eaton Jan 2008 - Oct 2011
Product Development Manager Engineering Specialist
Saint-Gobain 2004 - 2008
Product Development Manager
Saint-Gobain 2002 - 2007
Product Manager
Saint-Gobain Performance Plastics Oct 1997 - Aug 2002
Product Development and Applications Engineering Manager
Education:
Chatrapati Sahuji Maharaj Kanpur University, Kanpur 1990 - 1993
Master of Business Administration, Masters Ohio University Heritage College of Osteopathic Medicine 1980 - 1984
Euclid High School 1977 - 1980
Master of Business Administration, Masters Ohio University Heritage College of Osteopathic Medicine 1980 - 1984
Euclid High School 1977 - 1980
Skills:
Manufacturing
Product Development
Lean Manufacturing
Manufacturing Engineering
Continuous Improvement
Cross Functional Team Leadership
Engineering
Design For Manufacturing
Plastics
Extrusion
Engineering Management
Kaizen
5S
Materials
Process Engineering
Six Sigma
Manufacturing Operations Management
Product Management
Product Design
Fmea
Spc
Root Cause Analysis
Management
Value Stream Mapping
Iso
Polymers
Automotive
Operations Management
Injection Molding
Machine Tools
R&D
Industrial Engineering
Design of Experiments
Supplier Quality
Dmaic
Ts16949
Defining Product Requirements
Engineering Leadership
Ppap
Coatings
Apqp
Quality System
Quality Management
Process Simulation
Machining
Materials Science
Thermoplastics
Thermoforming
Stage Gate
Qs9000
Product Development
Lean Manufacturing
Manufacturing Engineering
Continuous Improvement
Cross Functional Team Leadership
Engineering
Design For Manufacturing
Plastics
Extrusion
Engineering Management
Kaizen
5S
Materials
Process Engineering
Six Sigma
Manufacturing Operations Management
Product Management
Product Design
Fmea
Spc
Root Cause Analysis
Management
Value Stream Mapping
Iso
Polymers
Automotive
Operations Management
Injection Molding
Machine Tools
R&D
Industrial Engineering
Design of Experiments
Supplier Quality
Dmaic
Ts16949
Defining Product Requirements
Engineering Leadership
Ppap
Coatings
Apqp
Quality System
Quality Management
Process Simulation
Machining
Materials Science
Thermoplastics
Thermoforming
Stage Gate
Qs9000