Resumes
Resumes
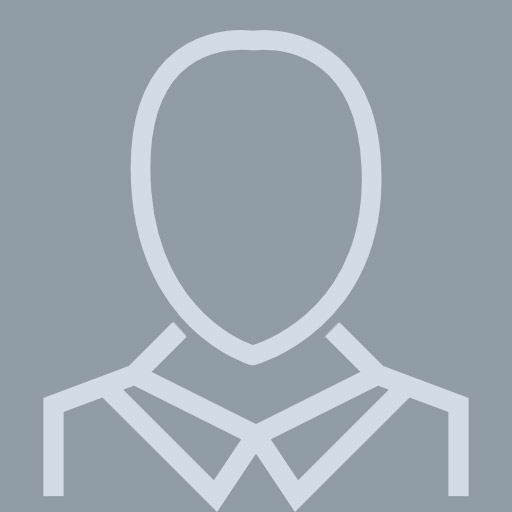
Erik Solyst
View pageLocation:
San Jose, CA
Industry:
E-Learning
Work:
Solyst
Retired
Retired