Professional Records
Medicine Doctors
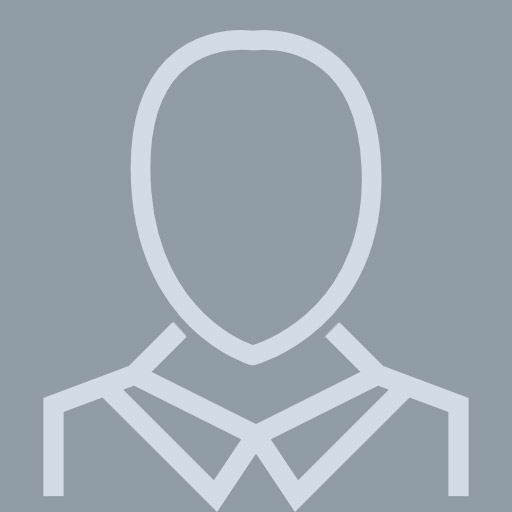
Eric M. Gifford
View pageSpecialties:
Orthopaedic Surgery
Work:
Ferrell-Duncan Bone & Joint Surgeons
3555 S National Ave STE 200, Springfield, MO 65807
(417) 875-3800 (phone), (417) 875-3176 (fax)
3555 S National Ave STE 200, Springfield, MO 65807
(417) 875-3800 (phone), (417) 875-3176 (fax)
Education:
Medical School
Med Univ of the Americas
Graduated: 2010
Med Univ of the Americas
Graduated: 2010
Procedures:
Electrocardiogram (EKG or ECG)
Vaccine Administration
Vaccine Administration
Conditions:
Acute Bronchitis
Acute Conjunctivitis
Acute Pharyngitis
Acute Sinusitis
Acute Upper Respiratory Tract Infections
Acute Conjunctivitis
Acute Pharyngitis
Acute Sinusitis
Acute Upper Respiratory Tract Infections
Languages:
English
Spanish
Spanish
Description:
Dr. Gifford graduated from the Med Univ of the Americas in 2010. He works in Springfield, MO and specializes in Orthopaedic Surgery. Dr. Gifford is affiliated with Cox Medical Center North and Cox Medical Center South.