Resumes
Resumes
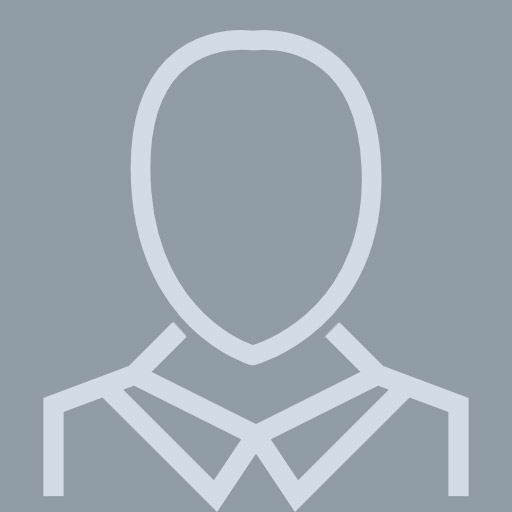
Edward Pietraszkiewicz
View pageLocation:
Hartford, CT
Industry:
Aviation & Aerospace
Work:
Parametric Solutions, Inc.
Chief Engineer - Turbine Airfoils Durability
Pratt & Whitney 1995 - Dec 2015
Principal Engineer - Turbine Airfoils Durability
Ge 1990 - 1995
Lead Engineer - Ge90 Turbine Aero Thermal
Chief Engineer - Turbine Airfoils Durability
Pratt & Whitney 1995 - Dec 2015
Principal Engineer - Turbine Airfoils Durability
Ge 1990 - 1995
Lead Engineer - Ge90 Turbine Aero Thermal
Education:
Rensselaer Polytechnic Institute - the Lally School of Management
Master of Science, Masters, Business Administration, Management, Business Administration and Management Worcester Polytechnic Institute
Bachelors, Bachelor of Science, Mechanical Engineering Rensselaer Polytechnic Institute at Hartford
Master of Science, Masters, Business Administration, Management, Business Administration and Management
Master of Science, Masters, Business Administration, Management, Business Administration and Management Worcester Polytechnic Institute
Bachelors, Bachelor of Science, Mechanical Engineering Rensselaer Polytechnic Institute at Hartford
Master of Science, Masters, Business Administration, Management, Business Administration and Management
Skills:
Aerospace
Engineering Management
Manufacturing
Engineering
Root Cause Analysis
Systems Engineering
Mechanical Engineering
Continuous Improvement
Finite Element Analysis
Machining
Aerospace Engineering
Turbines
Six Sigma
Lean Manufacturing
Earned Value Management
Propulsion
Pro Engineer
Ptc Creo
Airfoil Heat Transfer
Catia
Engineering Management
Manufacturing
Engineering
Root Cause Analysis
Systems Engineering
Mechanical Engineering
Continuous Improvement
Finite Element Analysis
Machining
Aerospace Engineering
Turbines
Six Sigma
Lean Manufacturing
Earned Value Management
Propulsion
Pro Engineer
Ptc Creo
Airfoil Heat Transfer
Catia