Resumes
Resumes
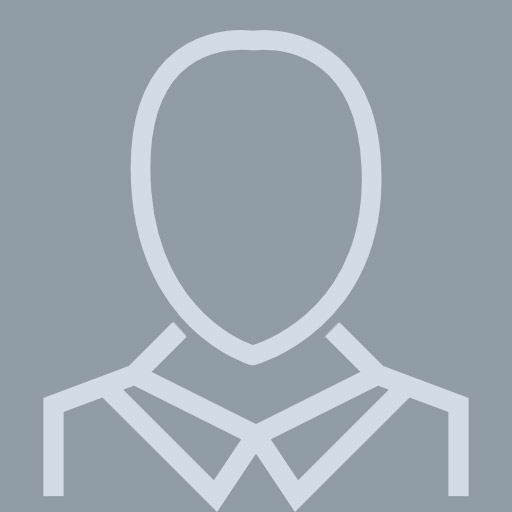
David Clingman
View page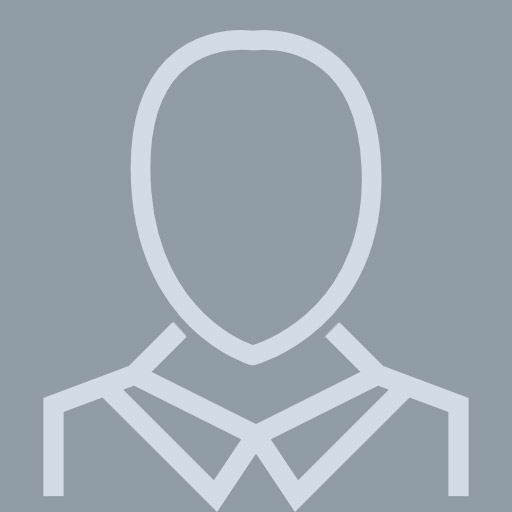
David Clingman
View pageLocation:
United States
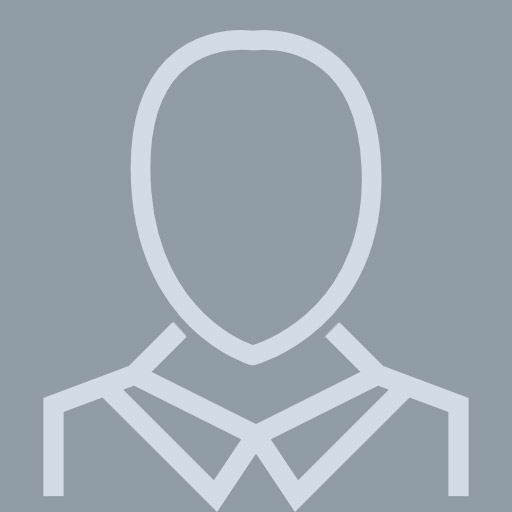
David Clingman
View pageLocation:
United States
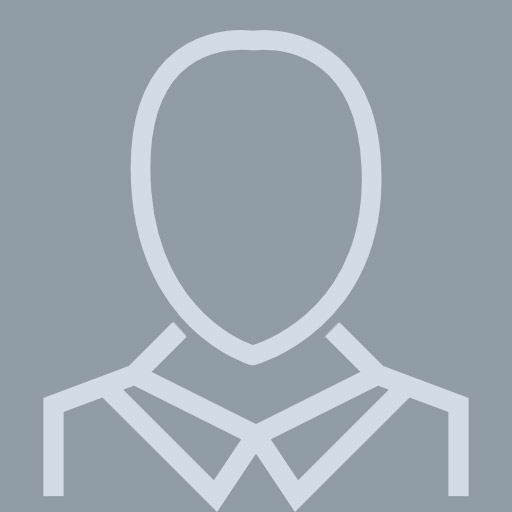
Owner At D-C Enterprises
View pageLocation:
Fresno, California Area
Industry:
Computer & Network Security
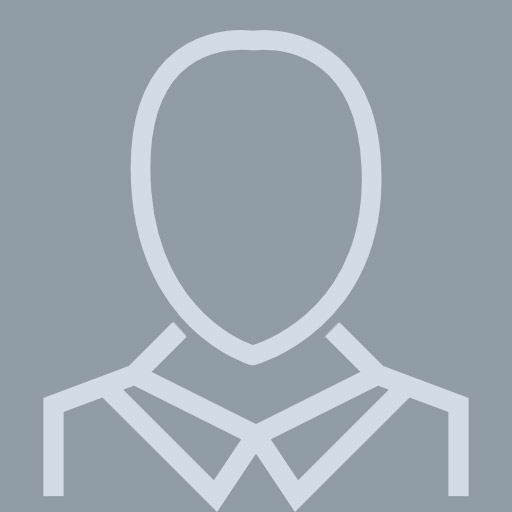
Owner/Manager At Great Web Gods
View pageLocation:
Fresno, California Area
Industry:
Computer Networking