Professional Records
Medicine Doctors
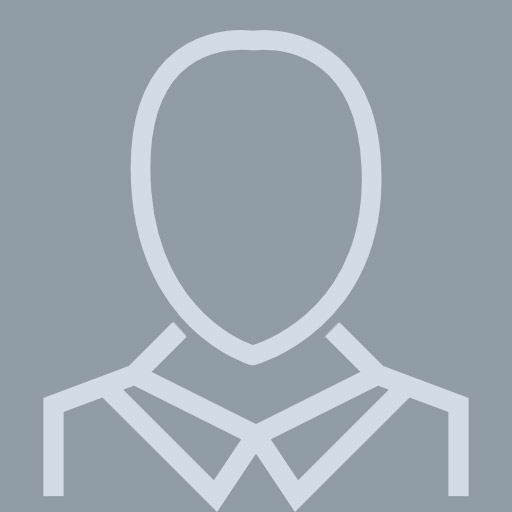
Christopher P. Cheney
View pageSpecialties:
Gastroenterology
Work:
Southcoast Physicians GroupSouthcoast Physicians Group Gastroenterology
208 Ml Rd Pod E, Fairhaven, MA 02719
(508) 973-2661 (phone), (508) 973-2665 (fax)
208 Ml Rd Pod E, Fairhaven, MA 02719
(508) 973-2661 (phone), (508) 973-2665 (fax)
Education:
Medical School
Uniformed Services University of the Health Sciences Hebert School of Medicine
Graduated: 1986
Uniformed Services University of the Health Sciences Hebert School of Medicine
Graduated: 1986
Procedures:
Esophageal Dilatation
Sigmoidoscopy
Upper Gastrointestinal Endoscopy
Colonoscopy
Sigmoidoscopy
Upper Gastrointestinal Endoscopy
Colonoscopy
Conditions:
Acute Pancreatitis
Benign Polyps of the Colon
Diverticulitis
Gastroesophageal Reflux Disease (GERD)
Inflammatory Bowel Disease (IBD)
Benign Polyps of the Colon
Diverticulitis
Gastroesophageal Reflux Disease (GERD)
Inflammatory Bowel Disease (IBD)
Languages:
English
Description:
Dr. Cheney graduated from the Uniformed Services University of the Health Sciences Hebert School of Medicine in 1986. He works in Fairhaven, MA and specializes in Gastroenterology. Dr. Cheney is affiliated with St Lukes Hospital.