Resumes
Resumes
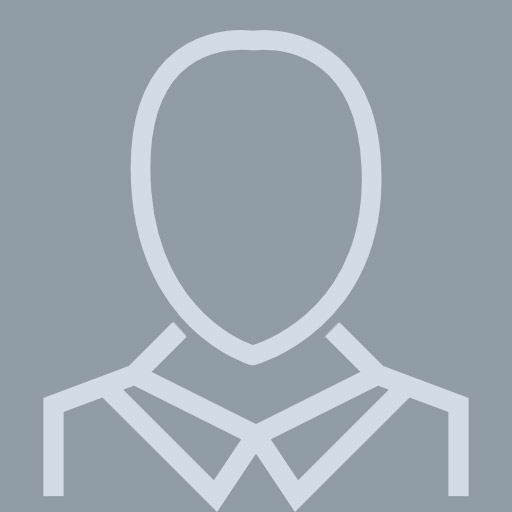
Product Manager
View pageLocation:
Oshkosh, WI
Industry:
Electrical/Electronic Manufacturing
Work:
Miller Electric Mfg. Co.
Product Manager
Product Manager
Skills:
Product Development
Product Management
Manufacturing
Product Marketing
Product Management
Manufacturing
Product Marketing