Resumes
Resumes
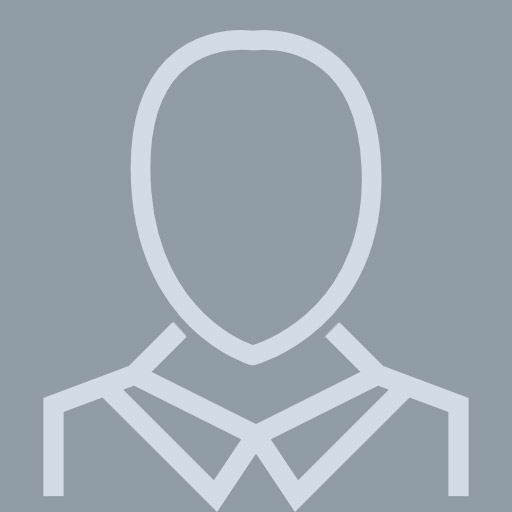
Billy Cagle
View pageWork:
Stewart Stainless Supply 2007 - 2013
Sales Representative
Sales Representative
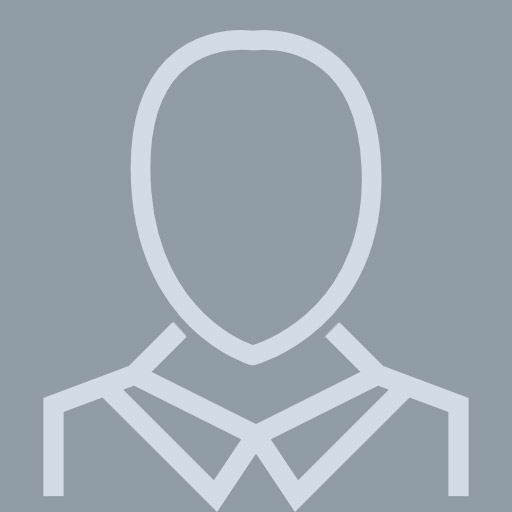
Billy Cagle
View page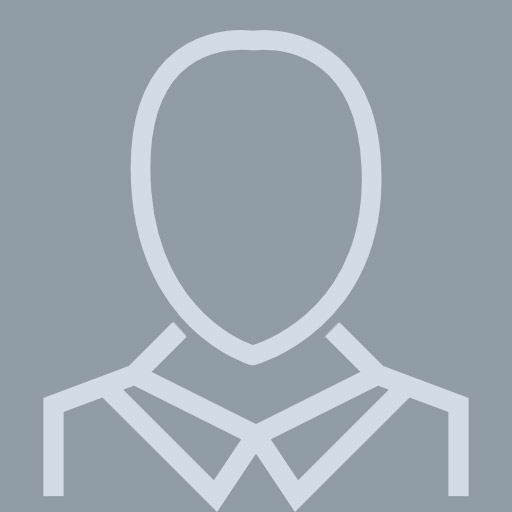
Billy Cagle
View page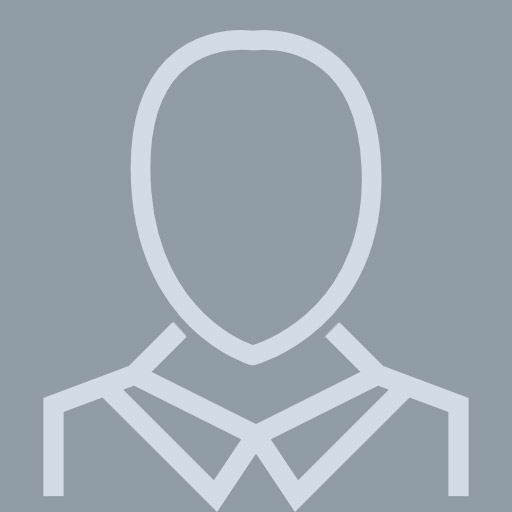
Billy Cagle
View page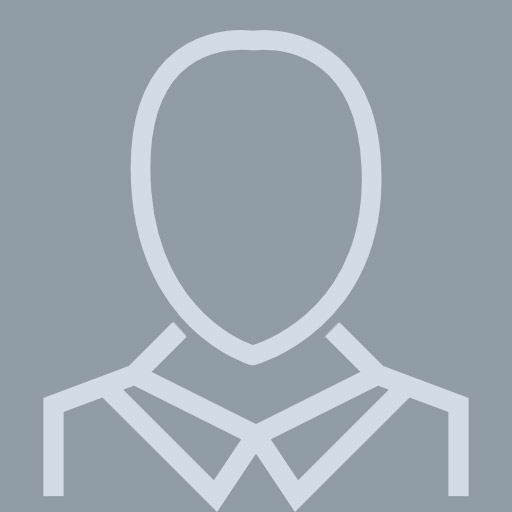
Billy Cagle
View page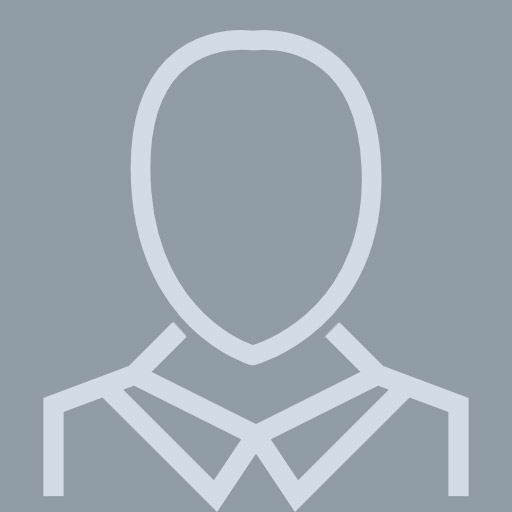
Billy Cagle Hazel Green, AL
View pageWork:
Laughlin Funeral Service
Jan 2008 to 2000
Laughlin Funeral Home an Crematory
Shaw Floors
Stevenson, AL
1994 to 2006
Factory Line Worker
Jan 2008 to 2000
Laughlin Funeral Home an Crematory
Shaw Floors
Stevenson, AL
1994 to 2006
Factory Line Worker
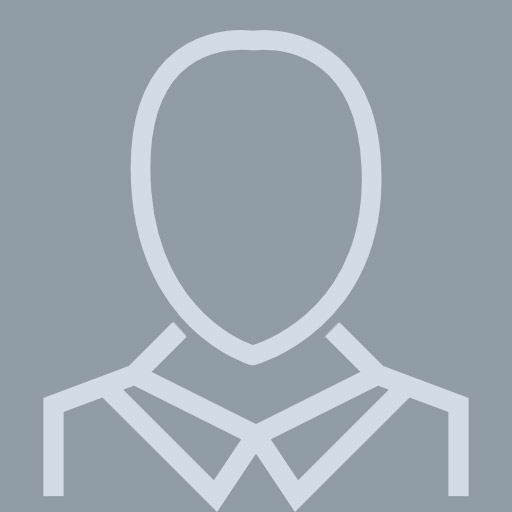
Billy Cagle
View pageLocation:
United States