Resumes
Resumes
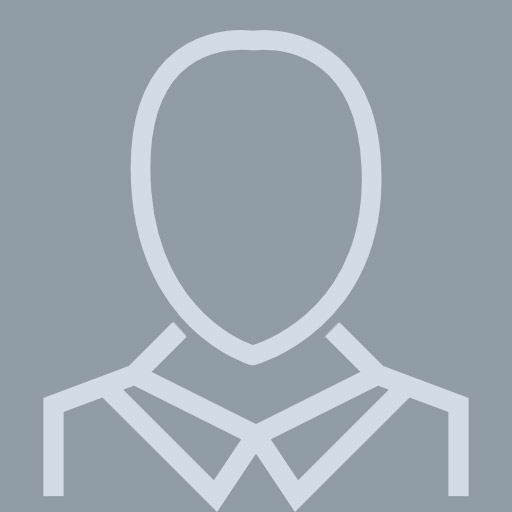
Manager
View pageLocation:
Pontiac, MI
Industry:
Automotive
Work:
Mootz Services
Manager
General Motors Mar 2006 - Mar 2015
Global Process Manager
Manager
General Motors Mar 2006 - Mar 2015
Global Process Manager
Education:
General Motors Institute 1974 - 1979
Bachelors, Bachelor of Science, Mechanical Engineering General Motors Institute {Kettering) 1974 - 1979
Bachelors, Bachelor of Science, Engineering, Mechanical Engineering
Bachelors, Bachelor of Science, Mechanical Engineering General Motors Institute {Kettering) 1974 - 1979
Bachelors, Bachelor of Science, Engineering, Mechanical Engineering
Skills:
Continuous Improvement
Automotive Engineering
Lean Manufacturing
Fmea
Value Stream Mapping
Process Improvement
Manufacturing Engineering
Process Engineering
Cross Functional Team Leadership
Program Management
Manufacturing
Supplier Quality
Quality Management
Pmp
Ppap
Kaizen
Failure Mode and Effects Analysis
Project Management
Automotive Engineering
Lean Manufacturing
Fmea
Value Stream Mapping
Process Improvement
Manufacturing Engineering
Process Engineering
Cross Functional Team Leadership
Program Management
Manufacturing
Supplier Quality
Quality Management
Pmp
Ppap
Kaizen
Failure Mode and Effects Analysis
Project Management
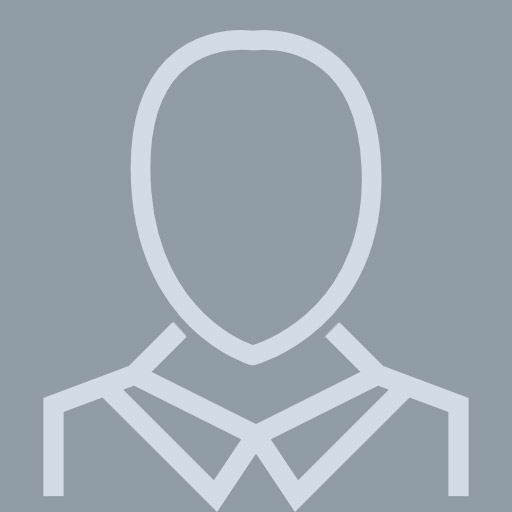
Barry Priem
View page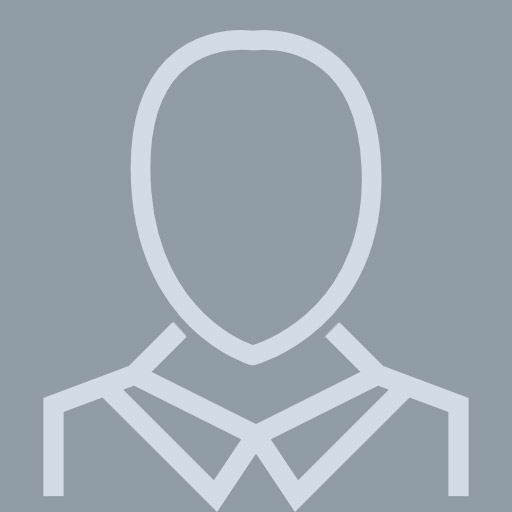