Resumes
Resumes
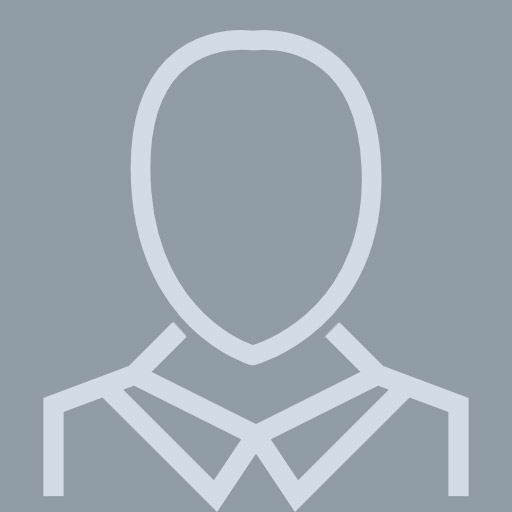
Amit Jayachandran Peoria, IL
View pageWork:
Caterpillar Inc
Mar 2013 to 2000
Engineering Project Manager/Test lead
Caterpillar Inc
Peoria, IL
Jan 2009 to Feb 2013
Six Sigma Black Belt-II
Caterpillar Inc
Peoria, IL
Oct 2006 to Jan 2009
Senior Engineer/Six Sigma Black Belt
Caterpillar Inc
Peoria, IL
Apr 2003 to Oct 2006
Engineer
Caterpillar Inc
Peoria, IL
Jul 2001 to Mar 2003
Senior Associate Engineer
NC State University
Raleigh, NC
May 1999 to Jun 2001
Research Assistant
Mar 2013 to 2000
Engineering Project Manager/Test lead
Caterpillar Inc
Peoria, IL
Jan 2009 to Feb 2013
Six Sigma Black Belt-II
Caterpillar Inc
Peoria, IL
Oct 2006 to Jan 2009
Senior Engineer/Six Sigma Black Belt
Caterpillar Inc
Peoria, IL
Apr 2003 to Oct 2006
Engineer
Caterpillar Inc
Peoria, IL
Jul 2001 to Mar 2003
Senior Associate Engineer
NC State University
Raleigh, NC
May 1999 to Jun 2001
Research Assistant
Education:
The University of Chicago, Booth School of Business
Chicago, IL
Jul 2013
MBA in Management, Entrepreneurship, International Business
North Carolina State University
May 1999 to Jul 2001
Masters in Mechanical Engg
Birla Institute of Technology and Science
Pilani, Rajasthan
May 1995 to Jun 1999
Bachelor of Engineering
Chicago, IL
Jul 2013
MBA in Management, Entrepreneurship, International Business
North Carolina State University
May 1999 to Jul 2001
Masters in Mechanical Engg
Birla Institute of Technology and Science
Pilani, Rajasthan
May 1995 to Jun 1999
Bachelor of Engineering